February 20, 2025 – Vancouver, British Columbia – Faraday Copper Corp. (“Faraday” or the “Company”) (TSX:FDY) (OTCQX:CPPKF) is pleased to announce the results of its metallurgical program for the Copper Creek project in Arizona (“Copper Creek”). The metallurgical program utilized samples from the Phase III drill program and was conducted by ALS Metallurgy (Kamloops, BC), with oversight by Ausenco Engineering.
The primary focus of the program was to evaluate the metallurgical performance of potential open pit mill feed material from the American Eagle area through coarse particle flotation across an extended spectrum of grind sizes. Application of a coarse grind and coarse particle flotation offers the potential to significantly increase mill throughput and reduce processing cost, compared to those contained in the Copper Creek Preliminary Economic Assessment (“PEA”)1.
This metallurgical program tested samples and composites from open pit domains by blending material types to determine performance ranges under various mill feed conditions. Expanding upon previous test work on the current resource area, the program was designed for comprehensive data collection related to grind size optimization, mineralogical composition, variability testing, conventional flotation and coarse particle flotation via hydrofloat.
Highlights
- Achieved copper rougher recoveries2 of 95.0% on a sulphide composite from the American Eagle area at a substantially larger grind size3 than that assumed in the PEA by applying Coarse Particle Flotation (“CPF”), resulting in the following potential benefits:
- Coarse grind and CPF can be used to maintain high copper recoveries across a full spectrum of feed grades. Applying a 350 micron (“µm”) primary grind with CPF scavenging returns comparable copper recovery to a conventional flotation circuit with a 200 µm primary grind3.
- Significant increase to mill throughput.
- Reduced ball mill grinding energy by approximately 50%.
- Continued to demonstrate excellent metallurgical performance on samples from the near-surface material at the American Eagle area, measuring locked cycle copper recoveries above 92% to a copper concentrate grade of approximately 31% copper.
- Metallurgical test work confirms a coarse grind and high copper recovery flowsheet with a highly marketable, clean concentrate.
- Data for the entire deposit supports the potential for low capital intensity and a favourable operating cost profile. This data will underpin future technical studies.
Zach Allwright, VP Projects and Evaluations, stated "The metallurgical results represent a pivotal point in the technical advancement of Copper Creek. The ability to maintain very high copper recoveries at a coarse primary grind across a wide range of feed grades demonstrates the near-term potential for enhanced project economics. The test work completed to date demonstrates that the mill throughput rate could be significantly increased in a capital efficient manner, while reducing operating costs and reinforcing our commitment to sustainability. We are excited to incorporate our recent drilling success and optimized flowsheet approach into an updated technical study in the second half of 2025.”
Next Steps
The outcomes of this program will be assimilated with historical test work to form the basis of the flowsheet design criteria and infrastructure considerations for future technical studies. The steps to continue to enhance the value of the project include:
- Exploration Drilling: Phase III drilling continues and is focused on growth of the open pit mineral resource. The Company has conducted over 30,000 metres of drilling since the last Mineral Resource Estimate was published1, with the discovery of new zones of mineralization and a portfolio of untested targets, this represents a significant opportunity to enhance the project value.
- Metallurgical Assessments: Test work will continue on new targets, as material becomes available, to maintain deposit-wide data coverage and ensure optimization opportunities are realized in future technical studies.
- Mineral Resource and Technical Report: The Company anticipates a data cut-off by the end of the first quarter of 2025 and the release of an updated technical study in the second half of 2025. This report will incorporate updated geological, geotechnical, economic and metallurgical datasets.
- Waste Rock Characterization: To complement existing material geochemical data and evaluations, laboratory and field-based characterization programs will take place to optimize waste management strategies.
- Environmental Data: The Company continues to expand its environmental baseline data collection program including water sampling, installation of additional monitoring wells, stream gauges, and piezometers in drill holes. The program also encompasses site-specific meteorological and air data collection, along with archaeological, cultural, flora and fauna studies.
Metallurgical Program Technical Details
Overview
The metallurgical program utilized samples from the Phase III drill program, to complement and expand upon previous test work as outlined in the PEA1. The metallurgical program was conducted by ALS Metallurgy (Kamloops, BC), with oversight by Ausenco Engineering.
This test work program was designed to complete the following scope with focus on the potential open pit mill feed material:
- Semi-Autogenous Grinding (“SAG”) mill comminution and Bond Mill Work Index (“BMWi”) testing completed on all samples.
- Mineralogical composition assessment on eight sulphide variability samples.
- Detailed mineralogy particle mineral analysis completed on sulphide master composite and coarse fractions of CPF sulphide composite.
- Flotation testing on sulphide composites and variability samples.
- Hydrofloat testing on a CPF sulphide composite.
The outcomes of this program will be integrated with the historical test work to form the basis of the process design criteria for the updated technical study expected to be released in the second half of 2025.
Sample Selection and Spatial Context
The metallurgical program comprised seven samples representing potential open pit material at the American Eagle area and Area 51, and one sample from Old Reliable. Two composites were compiled to challenge metallurgical performance and demonstrate deposit-wide application of coarse particle flotation. The American Eagle master composite was compiled from sulphide materials to reflect a lower grade composite than previously tested sulphide composites. The American Eagle area CPF composite was designed to reflect a lower grade mill feed scenario and a blend of approximately 50:50 breccia with vein-hosted mineralized material.
Samples were acquired from the Phase III drill program, which is focused on expansion of near-surface mineral resources in the American Eagle area.
Sample details are presented in Table 1 and sample locations are presented in Figure 1 below.
Table 1: Phase 3 Metallurgical Sample Details
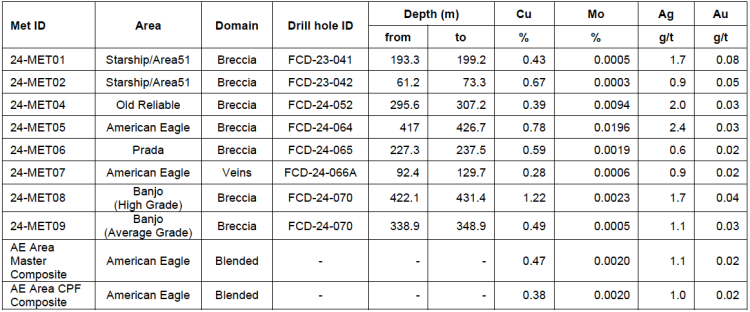
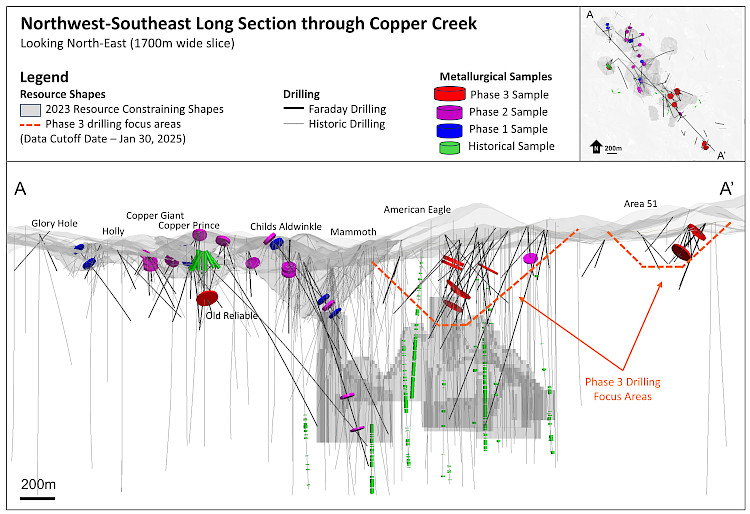
Comminution Results
SAG and ball mill energy assessment tests were conducted on the variability samples, which included industry standard SAG mill comminution and BMWi measurements, respectively. Results of the Phase 3 program and previous phases are presented in Table 2 below.
Table 2: Comminution Results
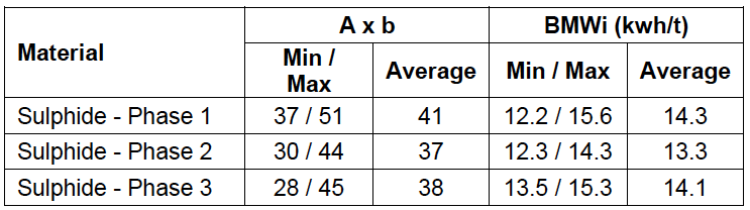
The outcomes of the comminution test work indicate that the new materials fall within the design tolerances of the PEA. The Old Reliable sample showed a higher resistance to impact breakage with an Axb value of 28, however the American Eagle area and Area 51 were similar to previous results. The BMWi results were similar to the averages measured in the previous programs, demonstrating consistent comminution expectations across the known deposits.
Flotation Performance – Sulphide Material
Flotation testing on the American Eagle area master composite (“MC”) culminated in a locked cycle test conducted at a primary grind size of 218 µm. Similar process conditions to the locked cycle test conducted in the Phase 2 program were applied to the Phase 3 program. Results are presented in Table 3 below.
Table 3: Locked Cycle Test Results

The American Eagle area master composite returned similar metallurgical performance as the two sulphide composites from the current open pit resource that were previously tested (refer to the Company’s news release dated February 26, 2024). Compared to the previously tested sulphide composites, the difference in copper recoveries can be attributed to the lower feed grade and slightly higher losses to the cleaner tailings. The near-surface samples of the American Eagle area have lower modelled molybdenum concentrations than at depth and in other areas of the deposit, and as a result, molybdenum recovery was not tracked in these flotation tests.
Open circuit cleaner flotation tests were conducted on each of the variability samples. The developed conditions were applied, which included low dosages of potassium amyl xanthate (“PAX”) as a collector, regrinding and up to three stages of dilution cleaning. Moderate dosages of lime were applied in the cleaner circuit.
Chalcopyrite is the dominant copper-bearing sulphide and occurs together with minor amounts of bornite; both recover well in a flotation circuit. This chalcopyrite dominant mineralization is representative of the American Eagle area and the wider open pit resource. Area 51 samples (24-MET01 and 24-MET02) contain chalcocite together with bornite, chalcopyrite and pyrite (Figures 1 and 5), which explains the different performance compared to the American Eagle area. Copper concentrate grades averaged 26% copper when including vein-hosted material from the American Eagle area and pyrite and chalcocite-rich breccia material from Area 51. Results are presented in Table 4 below.
Table 4: Phase 3 Cleaner Flotation Results
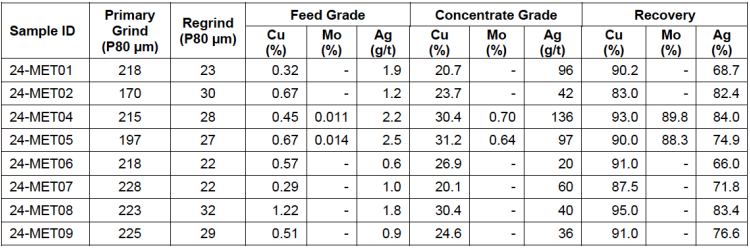
Molybdenum recovery was not targeted or tracked in a portion of these flotation tests as the feed grade was deemed too low to result in appreciable upgrading to the bulk flotation concentrate. Only two samples contained significant levels of molybdenum. In these two tests molybdenum recovery to the bulk concentrate averaged 89.1%.
Coarse Grind and CPF Performance Overview
Flotation performance at coarse primary grind sizes was investigated using conventional 4-litre and 30-litre Denver-type laboratory flotation cells, and a lab scale Eriez Hydrofloat cell. A composite was assembled with a greater portion of MET-07 sample (vein hosted mineralization), so that the feed material was lower grade, therefore, resulting in a more challenging composite for achieving high copper recoveries.
CPF is a technique that combines the upward flow of a hydrosizer with flotation bubbles to recover coarse mineralized particles that would otherwise report to tailings in conventional froth flotation. It can be applied in a scavenging application on rougher flotation tails that have passed through hydrocyclone size separation to remove lower grade fine material. The coarse material enters a hydrofloat cell, which recovers a coarse scavenger concentrate. The thickened underflow, depleted of any fines, is essentially free-draining and can be dewatered using a low energy system such as a sieve bend screen or a high-capacity belt filter.
Two bulk rougher flotation tests with hydrofloat scavenging were conducted on the Phase 3 CPF composite at primary grind sizes ranging from 300 µm to 330 µm. In addition, four conventional bench scale flotation tests were conducted over a wider primary grind size range. Results are presented in Table 5 and Figure 2, along with results from the Phase 2 program for comparison. Note that the Phase 2 composite originated from zones further north that were comprised of higher-grade samples and contained less vein hosted material.
Table 5: CPF Results Summary
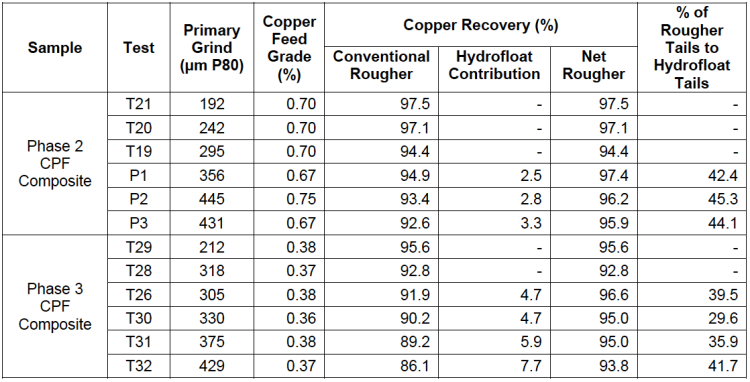
Notes to Table 5:
1. In tests with hydrofloat, conventional rougher tailings were classified such that approximately 50% of the mass reported to a +150 µm or +212 µm fraction with elevated copper levels. These coarse tailings were then treated in a laboratory hydrofloat cell which recovered an additional coarse concentrate.
2. Only the conventional rougher component of T31 and T32 were completed, hydrofloat results were estimated from assay by size data and T26 and T30 hydrofloat performance.
CPF performance confirms that a coarser grind can be applied to material originating from the American Eagle area without compromising copper recoveries. CPF may provide a greater recovery benefit to lower grade feeds that have more disseminated chalcopyrite textures, as demonstrated by the difference in performance compared to the Phase 2 composite. Applying CPF scavenging on the rougher tails of a 350 µm primary grind appears to return the same overall rougher circuit copper recovery as a conventional flotation circuit with a 200 µm primary grind as proposed in the PEA.
Figure 2: Coarse Grinding and CPF Performance
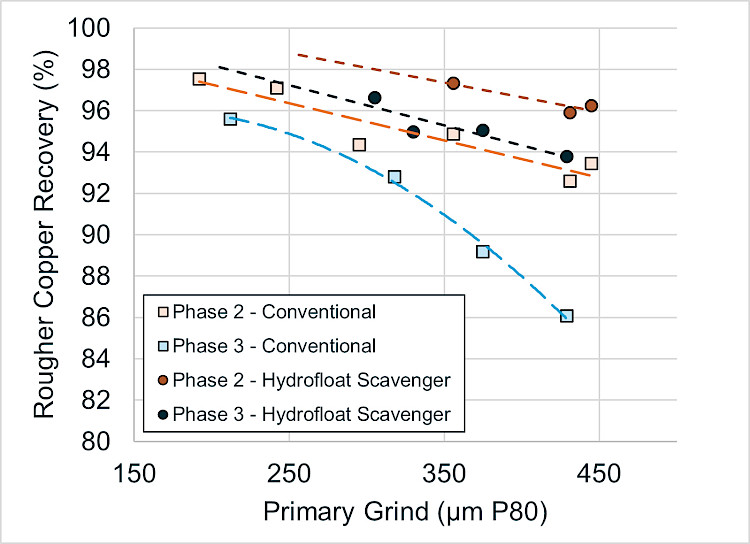
The CPF concentrate requires regrinding prior to returning to the rougher feed or similar conventional flotation stage. A simplified flowsheet incorporating CPF is presented in Figure 3.
Figure 3: Potential Coarse Grind Flowsheet
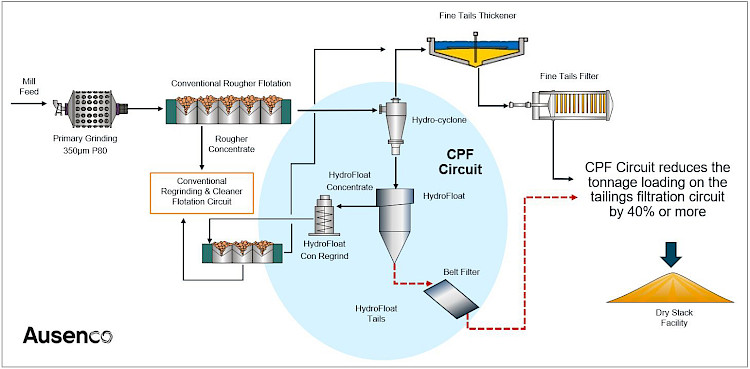
Additional grinding energy is only applied to a targeted 6% of the feed mass returning as CPF concentrate. While the incremental copper recovery improvement is modest, a significant benefit of the CPF circuit is removing tonnage from the tailings pressure filtration circuit. In this arrangement, approximately 57% of the total mill tailings report to the fines dewatering circuit. The free-draining hydrofloat tailings can be dewatered by more cost effective means1 such as a dewatering screen or a belt filter. The tailings processing opportunity of this flowsheet is presented in Figure 4. Preliminary results suggest that a CPF circuit could potentially allow for an increase in throughput to 45,000 tonnes per day or more without increasing the tailings pressure filtration requirements1.
Figure 4: Tailings Processing Comparison between PEA Conventional Flotation and CPF Addition
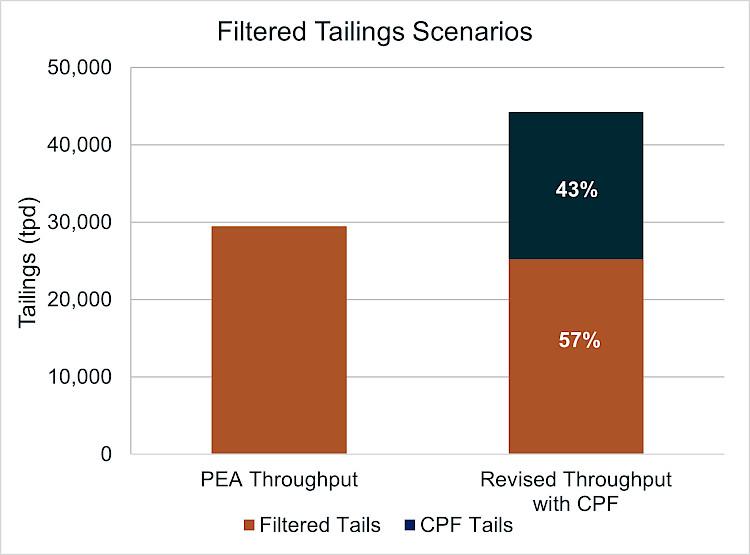
Concentrate Quality
Final bulk concentrates were assayed for minor elements of interest. Results are presented in Table 6 below. Two of the sulphide variability samples produced concentrates that contained sufficient molybdenum levels to support the inclusion of a copper-molybdenum separation circuit. The project considers that generation of a molybdenum concentrate may not be consistent over the mine life as not all areas are expected to have sufficient molybdenum in the feed. The proposed flowsheet and operation strategy incorporates flexibility to accommodate a molybdenum circuit that can be engaged in response to mill feed grade to maximize project value.
Gold in concentrate was elevated in sample MET-01, which was comprised of breccia hosted mineralization from the Starship breccia in Area 51. Gold contents in the American Eagle area concentrates were below minimum payable levels on average, while silver contents varied and were significant in some samples.
All arsenic contents were below penalty level limits and confirm previous test work, which concluded that the project demonstrated the potential to output a clean and highly marketable concentrate.
Table 6: Concentrate Quality of Variability Samples
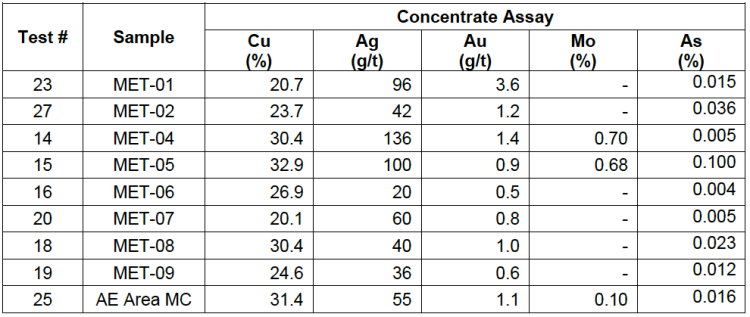
Note to Table 6: Other penalty elements such as antimony, bismuth and selenium were below penalty limits in the American Eagle area Master Composite. Mercury and fluorine were analyzed in the concentrate of a Phase 1 composite and also found to be low and below levels of smelter sensitivity and were therefore not investigated in this program.
Mineralogy Overview
Mineralogical composition assessments were completed on the variability samples by QEMSCAN. The results provide valuable confirmation of core logging interpretation and are consistent with geochemical assay results. The copper deportment data helps to understand metallurgical performance. Copper deportment by mineral is presented in Figure 5 below.
Figure 5: Copper Deportment by Mineral
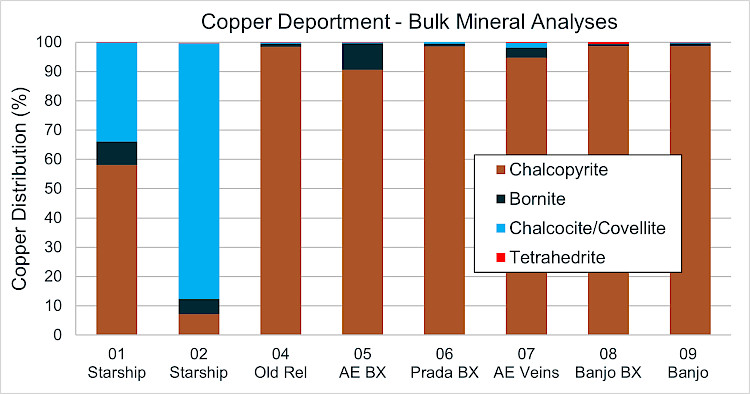
In the Old Reliable and American Eagle areas, copper is primarily contained in chalcopyrite, with minor amounts of bornite. In the Starship breccia at Area 51, more chalcocite and covellite is present.
The ratio of pyrite to copper sulphides can be an important processing parameter, as values below three tend to have lower regrinding energy requirements and positive implications on metallurgical performance. The pyrite to copper sulphide ratios of variability samples are displayed in Figure 6 relative to copper feed grade, along with values from sulphide samples tested in previous programs. Generally, the material is low in pyrite content, with 82% of the sulphide samples tested having ratios of pyrite to copper sulphides of less than 2:1.
Only two outliers with elevated pyrite exist in the sample set. These are MET-01 sample from the Starship breccia at Area 51 with elevated pyrite together with chalcocite, bornite and chalcopyrite, and a sample from the Bald zone (Phase 2 metallurgical program) which has pyrite and chalcopyrite.
Figure 6: Ratio of Pyrite to Copper Sulphides – Variability Samples
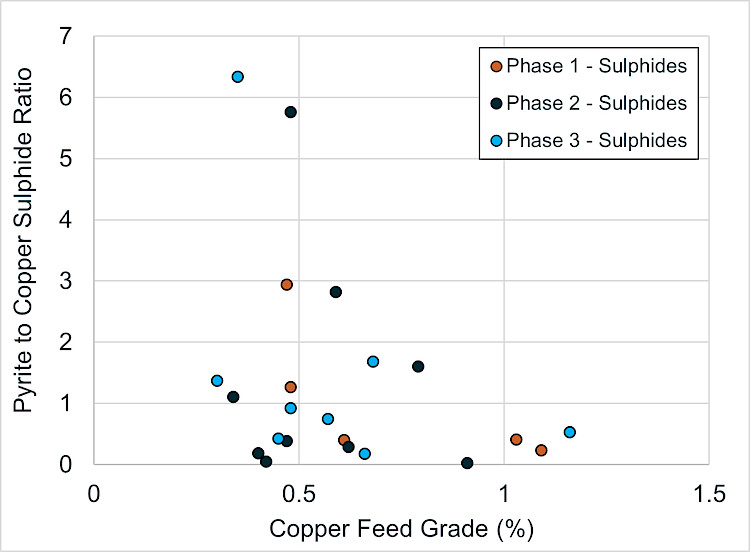
A more detailed particle mineral analysis was conducted on the CPF composite at a primary grind sizing of 318 µm. The liberation characteristics were favourable and supports the metallurgical performance measured in flotation tests. Specifically:
- The size distribution of the copper sulphide grains was coarse, measured at 149 µm P803.
- Although the overall copper sulphide mineral liberation was approximately 49%, about 87% of the mineral mass was in grains, which contained 50% or more copper sulphide mineral. The high quality of the grains allows for successful bubble attachment in froth flotation.
Qualified Person
The scientific and technical information contained in this news release has been reviewed and approved by Faraday’s Vice President, Projects and Evaluations, Zach Allwright, P.Eng., who is considered a Qualified Person under National Instrument 43-101 - Standards of Disclosure for Mineral Projects (“NI 43-101”).
The information in this news release relating to metallurgical test work results has been supervised, reviewed and verified by Mr. Peter Mehrfert, P.Eng., who is Ausenco Engineering’s consultant for Faraday Copper. Mr. Mehrfert is a qualified metallurgist and has sufficient experience, which is relevant to the management and interpretation of test work activities undertaken to qualify as Competent Person under NI 43-101.
End Notes
1 Information is presented in comparison with the Preliminary Economic Assessment, which was reported in a technical report titled “Copper Creek Project NI 43-101 Technical Report and Preliminary Economic Assessment” with an effective date of May 3, 2023, available on the Company’s website at www.faradaycopper.com and on the Company’s SEDAR+ profile at www.sedarplus.ca.
2 Rougher recovery refers to the percentage of valuable minerals recovered in the initial or primary stage of the flotation process.
3 Grind size refers to 350 µm P80 applied to the sulphide composite, compared to 190 µm P80 utilized in the PEA. Grind sizes stated throughout this news release refer to 80% passing (“P80”) the specified particle size.
About Faraday Copper
Faraday Copper is an exploration company focused on advancing its flagship copper project in Arizona, U.S. The Copper Creek project, is one of the largest undeveloped copper projects in North America with open pit and bulk underground mining potential. The Company is well-funded to deliver on its key milestones and benefits from a management team and board of directors with senior mining company experience and expertise. Faraday trades on the TSX under the symbol “FDY”.
For additional information please contact:
Stacey Pavlova, CFA
Vice President, Investor Relations & Communications
Faraday Copper Corp.
E-mail: info@faradaycopper.com
Website: www.faradaycopper.com
To receive news releases by e-mail, please register using the Faraday website at www.faradaycopper.com.
Cautionary Note on Forward Looking Statements
Some of the statements in this news release, other than statements of historical fact, are “forward-looking statements” and are based on the opinions and estimates of management as of the date such statements are made and are necessarily based on estimates and assumptions that are inherently subject to known and unknown risks, uncertainties and other factors that may cause actual results, level of activity, performance or achievements of Faraday to be materially different from those expressed or implied by such forward-looking statements. Such forward-looking statements and forward-looking information specifically include, but are not limited to, statements concerning project economics, timing of future Mineral Resource Estimate and Technical Report, the potential mill throughput, the expected copper concentrate quality, the potential for reduction in ball mill grinding energy, the expected copper, molybdenum, silver and gold recoveries, the possibility of adding gold in future Mineral Resource Estimates, capital intensity, the potential to reduce expected processing operating costs, and the exploration potential of the Copper Creek property.
Although Faraday believes the expectations expressed in such forward-looking statements are based on reasonable assumptions, such statements should not be in any way construed as guarantees of future performance and actual results or developments may differ materially. Accordingly, readers should not place undue reliance on forward-looking statements or information.
Factors that could cause actual results to differ materially from those in forward-looking statements include without limitation: market prices for metals; the conclusions of detailed feasibility and technical analyses; lower than expected grades and quantities of mineral resources; receipt of regulatory approval; receipt of shareholder approval; mining rates and recovery rates; significant capital requirements; price volatility in the spot and forward markets for commodities; fluctuations in rates of exchange; taxation; controls, regulations and political or economic developments in the countries in which Faraday does or may carry on business; the speculative nature of mineral exploration and development, competition; loss of key employees; rising costs of labour, supplies, fuel and equipment; actual results of current exploration or reclamation activities; accidents; labour disputes; defective title to mineral claims or property or contests over claims to mineral properties; unexpected delays and costs inherent to consulting and accommodating rights of Indigenous peoples and other groups; risks, uncertainties and unanticipated delays associated with obtaining and maintaining necessary licenses, permits and authorizations and complying with permitting requirements, including those associated with the Copper Creek property; and uncertainties with respect to any future acquisitions by Faraday. In addition, there are risks and hazards associated with the business of mineral exploration, development and mining, including environmental events and hazards, industrial accidents, unusual or unexpected formations, pressures, cave-ins, flooding and the risk of inadequate insurance or inability to obtain insurance to cover these risks as well as “Risk Factors” included in Faraday’s disclosure documents filed on and available at www.sedarplus.ca.
This press release does not constitute an offer to sell or a solicitation of an offer to buy any securities in any jurisdiction to any person to whom it is unlawful to make such an offer or solicitation in such jurisdiction. This press release is not, and under no circumstances is to be construed as, a prospectus, an offering memorandum, an advertisement or a public offering of securities in Faraday in Canada, the United States or any other jurisdiction. No securities commission or similar authority in Canada or in the United States has reviewed or in any way passed upon this press release, and any representation to the contrary is an offence.